Skip to content
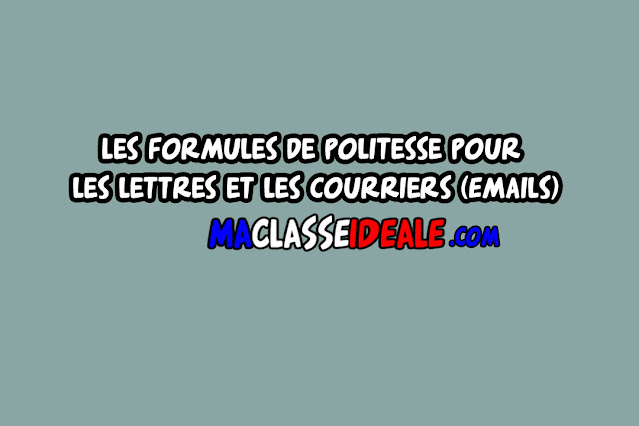
Les formules de politesse pour une lettre de motivation :
- Dans l’attente d’une réponse de votre part, je vous prie, Monsieur le Directeur, de bien vouloir recevoir mes plus respectueuses salutations.
- Dans l’attente de votre réponse, je vous prie d’agréer, Madame, Monsieur, mes sincères salutations.
- Dans l’attente d’une réponse que j’espère favorable, je vous prie de recevoir, Madame, Monsieur, mes salutations distinguées.
- Souhaitant que cette lettre de motivation retienne votre attention, je vous prie de croire, Madame, Monsieur, en ma considération distinguée.
Les formules de politesse pour un courrier cordial ou amical :
- Veuillez croire à mon meilleur souvenir.
- Recevez, avec toute mon amitié, mes salutations distinguées.
- Croyez, Madame, Monsieur, à mes sentiments les meilleurs
- Je vous prie de croire, Madame, Monsieur, en ma considération distinguée.
- Quelle formule de politesse pour une lettre administrative ? Je vous prie d’agréer, Madame, Monsieur, mes salutations distinguées
- Dans cette attente, je vous prie d’agréer, Madame, Monsieur, mes salutations distinguées
- Espérant une suite favorable, je vous prie d’accepter, Madame, Monsieur, l’expression de mes sentiments distingués
- En espérant une réponse rapide de votre part, je vous prie d’agréer, Madame, Monsieur, l’expression de mes sentiments distingués.
Les formules de politesse pour un supérieur hiérarchique, un client ou un fournisseur :
- Veuillez agréer, Madame, Monsieur, l’expression de mon profond respect.
- Veuillez recevoir, Madame, Monsieur, l’assurance de ma considération distinguée.
- Nous vous prions de croire, Monsieur, à l’expression de nos sentiments les plus dévoués.
- Dans l’attente de votre réponse, je vous prie d’agréer, Madame, Monsieur, l’expression de mes sentiments distingués.
Les formules de politesse pour écrire à la noblesse :
- Je vous prie de croire, Madame la duchesse/ Monsieur le duc, en l’expression des mes plus respectueuses salutations.
- Je vous prie de bien vouloir croire, mon altesse royale, en l’assurance de mes respectueuses et honorables salutations.
- Je vous prie de bien vouloir croire, mon altesse royale, en l’assurance de mes respectueuses et honorables salutations.
- Je vous prie d’agréer, Monsieur le Marquis, l’expression de mon respectueux souvenir.
- Je vous prie de bien vouloir agréer, Monsieur le Baron (ou Madame la Baronne), l’expression de mes honnêtes et respectueuses salutations.
Les formules de politesse pour écrire au président de la république :
- Veuillez agréer, Monsieur le Président de la République, l’hommage de mon profond respect.
- Je vous prie d’agréer, Monsieur le Président de la République, l’expression de ma très haute considération.
- Veuillez agréer, Monsieur le président de la République, l’expression de ma respectueuse considération
Les formules de politesse pour une lettre de motivation :
- Dans l’attente d’une réponse de votre part, je vous prie, Monsieur le Directeur, de bien vouloir recevoir mes plus respectueuses salutations.
- Dans l’attente de votre réponse, je vous prie d’agréer, Madame, Monsieur, mes sincères salutations.
- Dans l’attente d’une réponse que j’espère favorable, je vous prie de recevoir, Madame, Monsieur, mes salutations distinguées.
- Souhaitant que cette lettre de motivation retienne votre attention, je vous prie de croire, Madame, Monsieur, en ma considération distinguée.
Les formules de politesse pour un courrier cordial ou amical :
- Veuillez croire à mon meilleur souvenir.
- Recevez, avec toute mon amitié, mes salutations distinguées.
- Croyez, Madame, Monsieur, à mes sentiments les meilleurs
- Je vous prie de croire, Madame, Monsieur, en ma considération distinguée.
- Quelle formule de politesse pour une lettre administrative ?
- Je vous prie d’agréer, Madame, Monsieur, mes salutations distinguées
- Dans cette attente, je vous prie d’agréer, Madame, Monsieur, mes salutations distinguées
- Espérant une suite favorable, je vous prie d’accepter, Madame, Monsieur, l’expression de mes sentiments distingués
- En espérant une réponse rapide de votre part, je vous prie d’agréer, Madame, Monsieur, l’expression de mes sentiments distingués.
Les formules de politesse pour un supérieur hiérarchique, un client ou un fournisseur :
- Veuillez agréer, Madame, Monsieur, l’expression de mon profond respect.
- Veuillez recevoir, Madame, Monsieur, l’assurance de ma considération distinguée.
- Nous vous prions de croire, Monsieur, à l’expression de nos sentiments les plus dévoués.
- Dans l’attente de votre réponse, je vous prie d’agréer, Madame, Monsieur, l’expression de mes sentiments distingués.
Les formules de politesse pour écrire à la noblesse :
- Je vous prie de croire, Madame la duchesse/ Monsieur le duc, en l’expression des mes plus respectueuses salutations.
- Je vous prie de bien vouloir croire, mon altesse royale, en l’assurance de mes respectueuses et honorables salutations.
- Je vous prie de bien vouloir croire, mon altesse royale, en l’assurance de mes respectueuses et honorables salutations.
- Je vous prie d’agréer, Monsieur le Marquis, l’expression de mon respectueux souvenir.
- Je vous prie de bien vouloir agréer, Monsieur le Baron (ou Madame la Baronne), l’expression de mes honnêtes et respectueuses salutations.
Les formules de politesse pour écrire au président de la république :
- Veuillez agréer, Monsieur le Président de la République, l’hommage de mon profond respect.
- Je vous prie d’agréer, Monsieur le Président de la République, l’expression de ma très haute considération.
- Veuillez agréer, Monsieur le président de la République, l’expression de ma respectueuse considération
Scroll to Top